As a core maintenance equipment in the railway track system, the rail grinder is like a skilled "rail shaper" that performs precision processing on the rail surface through high-precision grinding wheel cutting operations. It can not only repair various rail surface damages but also optimize the wheel-rail contact relationship, serving as a key guarantee for ensuring the smooth operation of trains and extending the service life of rails.
Core Functions and Application Scenarios of Rail Grinding Machine
The core role of the rail grinding machine is to effectively address three major types of track defects through controlled cutting operations. Firstly, it can accurately repair surface damages on the rail, such as eliminating tread fatigue cracks with a depth of no more than 0.5 mm and spalling blocks with an area within 5 cm², thus preventing these damages from developing into potential fractures. Secondly, it can optimize the rail head profile by correcting the worn and deformed rail head according to design standards (e.g., the 1:40 rail top slope for 60 kg/m rails), strictly controlling the wheel-rail contact point within ±15 mm of the rail top center, and reducing wheel-rail force fluctuations by over 30%. Additionally, for short-wave irregularities such as rail vertical deviations and corrugation with wavelengths of 1-3 meters and amplitudes of no less than 0.3 mm, the rail grinding machine can achieve a longitudinal smoothness of the rail surface with a maximum deviation of 0.1 mm per meter through fine grinding.
Its applications cover the entire life cycle of railway operations: pre-grinding before the opening of new lines (to remove rolling scale), preventive grinding during operation (once every 500,000-800,000 gross ton-kilometers), and restorative grinding after the occurrence of defects (such as when side wear on curves exceeds limits).
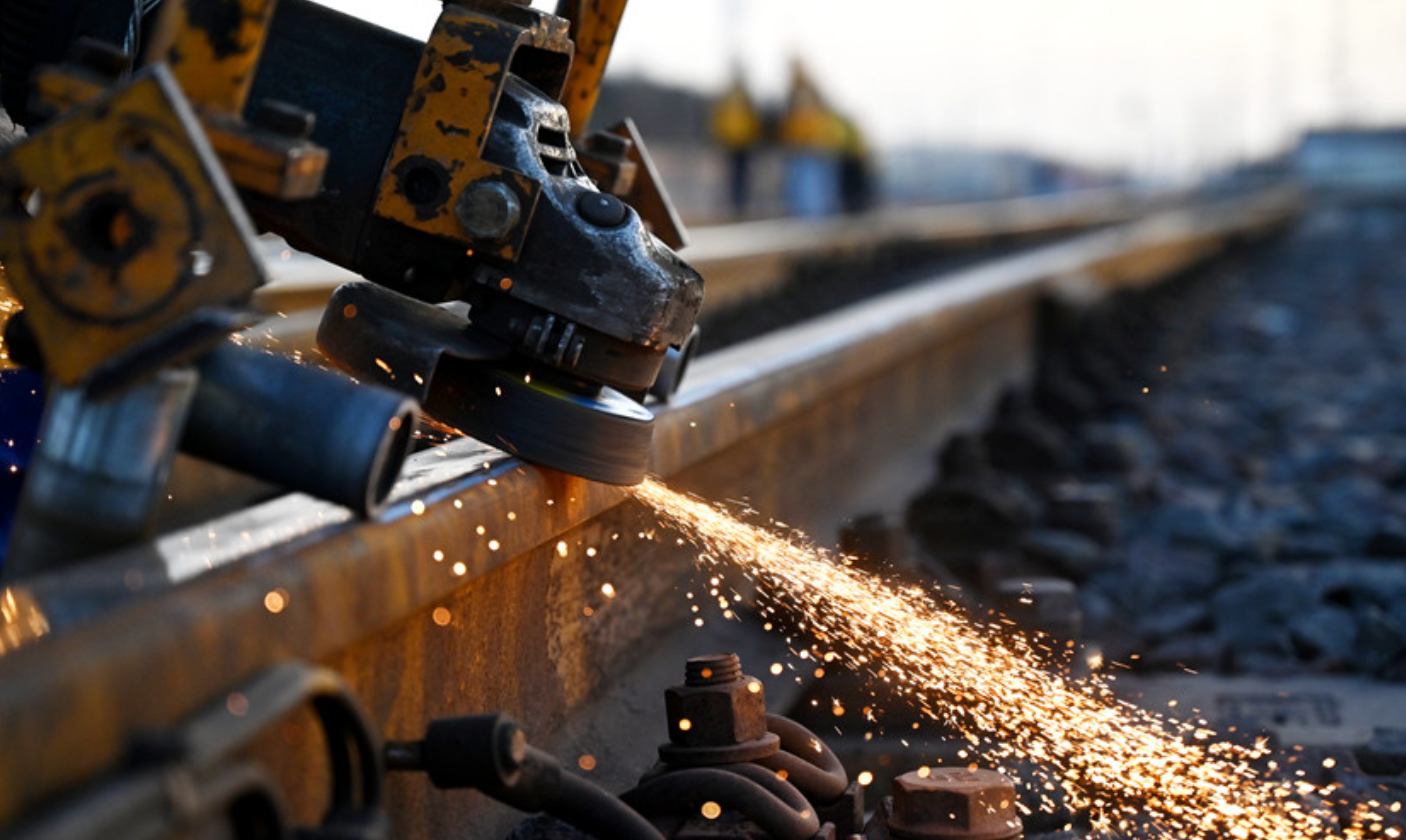
Main Types and Technical Features of Rail Grinding Machine
Based on operation scale and precision requirements, rail grinders are mainly divided into three categories:
Large-Scale Rail Grinding Trains
As the main equipment for line maintenance, large-scale rail grinding trains are usually equipped with 16-40 grinding wheels with diameters ranging from 350-400 mm. These grinding wheels are controlled independently in groups and can fully cover the entire cross-section of the rail for grinding operations. They can operate at speeds of 5-15 km/h, with a single grinding depth of 0.1-0.3 mm, and achieve a profile accuracy of 0.01 mm, with a deviation from the design value not exceeding 0.1 mm. Typical models of this type include Germany's LINSINGER 4000 (equipped with 40 grinding wheels) and China's Jinying GM-48 (equipped with 24 grinding wheels), which are widely used for full-range grinding operations on main railway lines.
Small-Scale Grinders
Small-scale grinders are mainly used for local precision processing, equipped with 2-4 grinding wheels, and can be operated manually or semi-automatically. They weigh between 50-200 kg and are equipped with dust suction devices to control dust concentration within 2 mg/m³. With an operating speed of 0.5-2 km/h and a single grinding depth not exceeding 0.1 mm, they are ideal for operations in areas inaccessible to large equipment, such as turnout areas and around welds. They are often used to repair local defects like switch tongue edge (with a thickness of no less than 1 mm) and weld depression (with a drop of no less than 0.3 mm).
Specialized Grinding Equipment
Specialized grinding equipment is customized to meet specific grinding needs. For example, profile grinders can adaptively adjust the grinding angle (within the range of 0°-30°) according to the measured profile when dealing with rail side wear in curved sections (with a wear amount of no less than 8 mm); weld grinders are equipped with 120# diamond grinding wheels to perform 0.05 mm-level precision grinding on welded joints, ensuring that the transition smoothness between the weld and the base metal does not exceed 0.1 mm/m.
Technical Trends: Intelligence and Precision
Nowadays, modern rail grinding machines are transforming from traditional "experience-based operation" to "data-driven" intelligence. Intelligent planning systems, combined with big data from rail inspection vehicles, can automatically generate grinding plans. For instance, for the outer rail side wear area in curves, they can automatically plan the grinding wheel angle and grinding amount distribution, with a plan accuracy of over 95%. The real-time closed-loop control system enables the grinding wheel set, equipped with force sensors and laser rangefinders, to dynamically adjust the grinding pressure with a response time of no more than 0.5 seconds, effectively compensating for cutting amount fluctuations caused by rail irregularities. In addition, comprehensive upgrades have been made in environmental protection, with efficient dust removal systems featuring a filtration efficiency of no less than 99.9%, and noise controlled below 85 decibels (at a distance of 10 meters from the equipment), meeting environmental protection requirements for operations in residential areas.